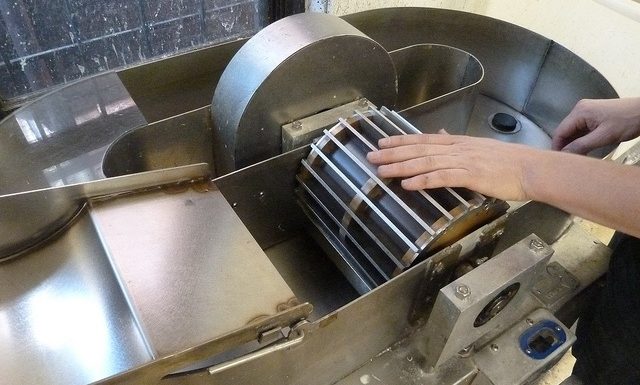
The Pulp and Paper is watching carefully as vendors such as Siemens, GE and SAP are aggressively pursuing manufacturing facilities with the promise of Industry 4.0 and the Smart Factory.
The issue for many plant owners is not whether to embrace digitalization but how to do so in a way that protects and improves upon current factory yields. At a strategic level, there is very little disagreement about the value of big data, machine learning, and the Digital Twin. The promise of extracting and operationalizing factory asset data in real time is compelling.
Today most of the Pulp and Paper Industry still uses the traditional SCADA rule-based monitoring systems. These traditional systems are not designed to process vast amounts of data in real time. That means that only 10% to 15% of a facility’s sensors can be monitored. More importantly, SCADA monitoring is based on a set of pre-defined rules or control limits that are hard coded by human engineers.
Attend a conference or read a trade publication and you will quickly find out that machine learning is one of the biggest buzzwords in the industry.GE Predix and Siemens MindSphere are positioning their Machine Learning platform as the vehicle to move to the Smart Factory.
For facility owners, the enthusiasm for change needs to be balanced with the economic reality that the so-called Digital Twin may not be viable today. The Digital Twin can provide a real-time virtual view of the physical performance of the machine and identify abnormal machine behavior. The major drawback is that the Digital Twin is not scalable for most industrial plants because it uses a Supervised Machine Learning methodology.
Supervised Machine Learning means that the algorithm needs to “learn” the machine behavior from the data labels of historic downtime records. A complete and accurate 3D modeling using the asset’s blueprints is needed. Once the Digital Twin is created, the learning algorithm can “learn” the workings of the machine to be able to duplicate its behavior.
Unfortunately, to deploy the Digital Twin, an army of external consultants, big data scientists and CAD technicians will need to work together with the factory’s maintenance and engineering staff. One sometimes overlooked requirement is that to create the virtual clone of a machine the exact blueprints are needed. If the blueprints are outdated because they do not include modifications, they will first need to be updated to be used.
Putting aside the cost in terms of financial and human resources, there are some plant owners hesitant to move to the Supervised Digital Twin because there is much uncertainty about which of the vendors will ultimately prevail in the marketplace. As GE and Siemens battle to dominate the space, many factories are taking a back seat and watching carefully. For many, the fact that these vendors have not been willing to provide detail product roadmap information is of major concern.
Another approach to Machine Learning is the Unsupervised Machine Learning approach that has started to gain attention in both the media and academic arenas. Based on the most advanced Artificial Algorithms, Machine Learning extracts all the sensor data from a Pulp and Paper factory and analyzes the data in real-time.
What’s important is that the Machine Learning approach is agnostic to machine type, asset class or sensor. It does not matter whether the machine is a Fourdrinier Machine manufactured by Beloit or a General Electric Turbine. Whether the sensor detects temperature, pressure or vibration is not a consideration because the Unsupervised Learning algorithm is designed to detect anomalous behavior and then to find correlations and patterns of anomalous behavior.
Both the Supervised (Digital Twin) and Unsupervised approach to Machine Learning are valuable additions to the Smart Factory and each has its role. The issue for today’s Pulp and Paper manufacturer is whether to wait until the Digital Twin becomes more affordable and the vendors more likely to share their product roadmap. The alternative route of Unsupervised Machine Learning can provide today’s Smart Factory with the advanced functionality and capabilities of the Digital Twin without the significant resource investment.