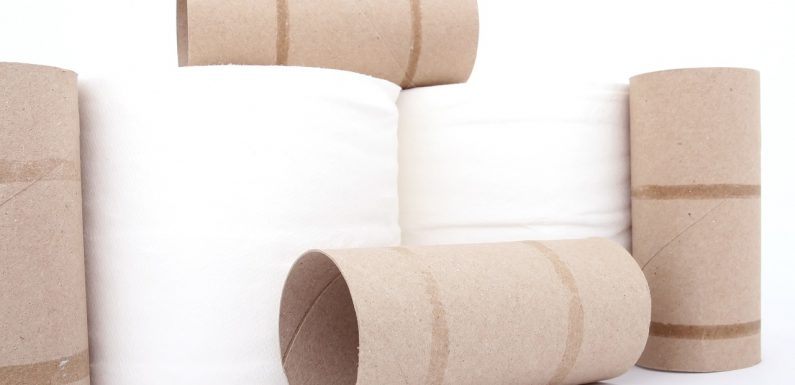
Tissue paper is a lightweight paper, or a crepe paper, which can be made from recycled paper pulp among other materials. It is mainly defined by its softness and fabric like feel.
The tissue paper manufacturing process only varies slightly from that of other papers.
It goes through the same underlying pulping, pressing and converting processes as regular paper, with minute changes.
Tissue Paper Processing
Pulping
- Trees are logged and cut into chips, which are then are ground into fine flakes, which are then soaked and pulled-apart (retted). Paper pulp is generated from wood fibre or recycled materials.
- Stirring together these fine retted flakes in a mixer tank with a large quantity of water and other chemicals generates.
- The manufacturer adds chemicals such as sodium sulphide, limestone, and others while the wood pulp is still in the mixing tank, to soften, strengthen or colour the paper.
Pressing
- The prepared pulp is then poured over fast moving belts made from highly porous materials that are driven over huge drums heated by steam. The pulp is poured uniformly and consistently across the width of the belt/drum. All the water escapes through the pores, leaving just the fibres on the belt in the form of a delicate fabric.
- The tissue is then transferred on to a massive heated roller called a Yankee. The heat of the Yankee makes the fabric dry almost instantly.
- The tissue paper is then transferred on to a core to form a large diameter roll.
- Adjust the draw speed of the roll can let you get a thicker or thinner tissue as per your goal.
- The rolls are then put onto the converting machine.
Converting
- The tissue is taken and its plies are split and passed through an embossing roller.
- Embossing softens the toilet tissue and can be used to create decorative patterns.
- The plies are removed and held together with glue. The tissue is then perforated by doctor blades, enabling the sheets to be easily pulled apart.
- The tissue can then be made into either flat surfaces or wound around a cardboard tube to create a cylindrical rolls.
- Many different roll sizes and sheet counts are produced on the winding machines.
- The large roll is fed into a doctoring system and cut by a large rotating doctor blade into individual rolls.
Properties of Tissue Paper
Key properties of tissue paper manufacturers target include absorbency, basis weight, thickness, brightness, specific volume, and aesthetics.
Adjusting these properties makes it useful in various applications including hygiene and packaging.
Uses of Tissue Paper
Tissue papers come in varying thicknesses and textures but are primarily used as hygienic (anti-bacterial) tissues, facial tissue, toilet tissue, paper towels, table napkins and, sometimes, acoustic disrupters, and packing tissue.